From the elegance of wooden hulls to the modern embrace of fiberglass, aluminum, and advanced composites, the history of hull design reflects a commitment to enhancing performance, seaworthiness, and aesthetics.
The Early Days
Classic forms of hull design characterized the naval architecture of yesteryear, with vessels being created that seamlessly combined form with function. The sweeping lines and sleek profiles of these early designs not only worked in the waves, but they were also a testament to the craftsmanship that defined the era.
Boat makers would carefully select oak, teak, and mahogany as these were revered for their strength, durability, and resistance to the corrosive effects of seawater. Before a single plank touched the boat's frame, however, the lofting process would be carried out — a series of measurements and lines that translated a boat's design onto a lofting floor. Here, boatmakers would meticulously draw full-scale patterns, ensuring every curve and contour mirrored the designer's vision. This blueprint would subsequently be used as the plan for the build stage ahead.
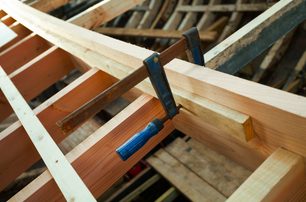
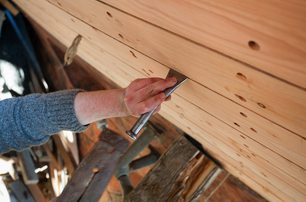
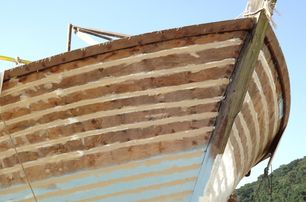
The joinery phase was the soul of wooden boat making, where the craftsmanship of the boatmaker truly shone. Scarf joints, dovetails, and mortise-and-tenon connections would be used to unite the boat's structural elements. Each joint would have been carefully crafted and secured with wooden pegs, ensuring longevity for the finished vessel.
Next up, planking. Armed with adzes and planes, craftsmen would transform bare frames into the recognizable form of a boat, with each plank being carefully shaped and fitted to the frame using the age-old technique of caulking and riveting. Eventually, a hull would be formed.
These vessels prioritized stability and seaworthiness, laying the aesthetic and structural foundations for the sophisticated yachts we admire today.
The Fiberglass Revolution
The mid-20th century heralded a transformative era in yacht construction, characterized by the groundbreaking introduction of fiberglass as a revolutionary hull material. This momentous shift marked not only a departure from traditional wooden hulls but also a profound change in the very fabric of yacht design, construction, and maritime technology.
Fiberglass, a composite material composed of fine glass fibers embedded in a matrix of resin, offered a compelling alternative to the conventional wooden hulls that had long dominated the seas. The use of fiberglass presented a myriad of advantages, including exceptional strength, durability, and resistance to corrosion — qualities that were paramount.
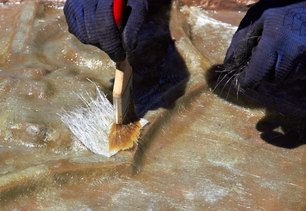
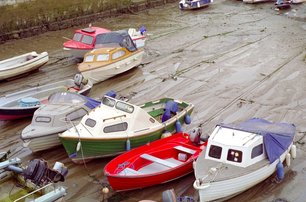
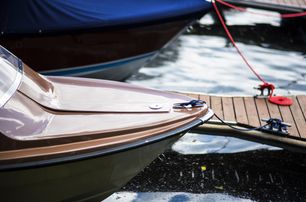
One of the most profound impacts of fiberglass was the newfound freedom it bestowed upon yacht designers. Unlike wood, fiberglass allowed for greater flexibility in shaping hulls, enabling designers to explore innovative and dynamic forms that were previously unattainable. The malleability of fiberglass opened the door to sleeker profiles and resulted in improved hydrodynamics.
Fiberglass quickly gained favor among yacht enthusiasts for its inherent durability and low maintenance requirements. Unlike wooden hulls that demanded meticulous care and were susceptible to rot, decay, and marine pests, fiberglass offered a resilient solution. Yachts crafted from fiberglass became known for their longevity, reducing the need for extensive and labor-intensive upkeep.
The advent of fiberglass ushered in an era of mass production, making yachting more accessible to a broader audience. The streamlined manufacturing process allowed for quicker and more cost-effective production of fiberglass hulls compared to traditional wooden boat building methods.
The Need for Speed
With enthusiasts wanting to go faster, yacht design witnessed a paradigm shift with the ascension of planing hulls. Defined by a flatter bottom, these hulls revolutionized the sailing experience by allowing vessels to rise onto the water's surface at higher speeds. This innovation significantly reduced drag, enhancing overall performance and maneuverability. Planing hulls, particularly prevalent in the motor yacht sector, provided users with exhilarating experiences, blending speed with exceptional handling capabilities.
At the core of planing hulls is a departure from traditional hull shapes. The introduction of a flatter bottom allowed vessels to defy conventional constraints, dynamically rising onto the water's surface. This departure from the customary V-shaped hulls set the stage for a new era in yacht design, emphasizing interaction between form and function

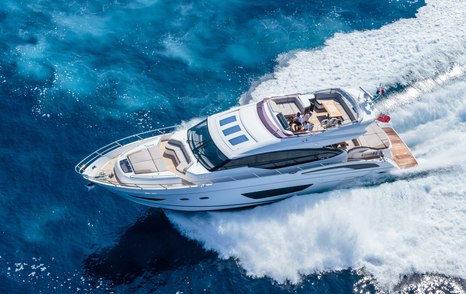
The true brilliance of planing hulls lies in their ability to dramatically reduce drag. As vessels ascend onto the water's surface, the minimized drag propels them forward with increased speed and efficiency. This seamless integration of design and hydrodynamics results in enhanced performance.
The planing hull also redefined maneuverability, with the flattened bottom and other design considerations, bestowing exceptional handling capabilities onto vessels. Nowhere is the mastery of planing hulls more evident than in the motor yacht sector. These vessels, equipped with planing hulls, not only exude a modern aesthetic, but they also deliver unparalleled on-water performance.
Aluminum Hull Design
Since first being used to build a steam launch vessel in 1891, aluminum has proved to be a popular material for producing hulls. Its lightweight nature improves fuel efficiency and overall performance, allowing faster speeds and better handling. Despite being lightweight, aluminum boasts a high strength-to-weight ratio, ensuring structural integrity and resistance to fatigue.
Another notable feature is aluminum's inherent corrosion resistance, forming a protective oxide layer that makes it suitable for saltwater environments and reduces the need for extensive maintenance. Its weldability facilitates the construction of complex and precisely engineered hull shapes, contributing to the creation of sleek, efficient vessels such as Genesis (below, previously called Galactica) produced by Heesen.
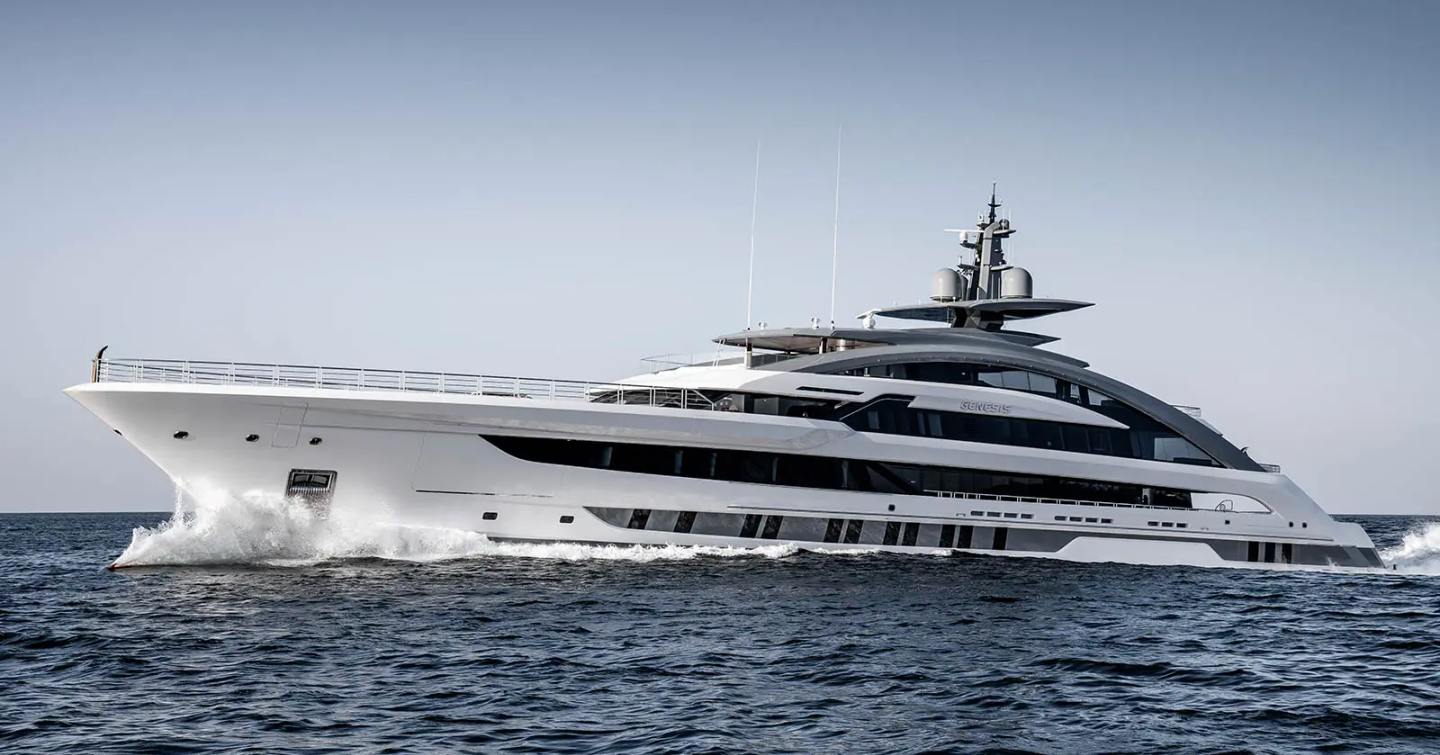
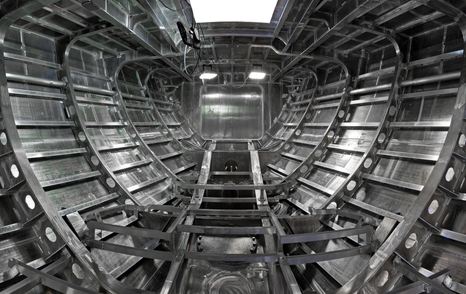
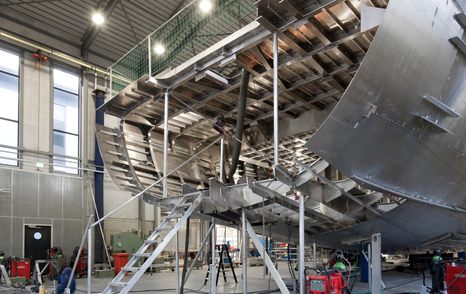
In the event of damage, aluminum hulls are often easier to repair than other materials, using welding techniques for localized issues. The material's recyclability also supports sustainability in the marine industry at the end of a vessel's life.
While aluminum hulls offer numerous advantages, proper engineering, anti-corrosion measures, and appropriate material thickness are crucial considerations for longevity and performance. The choice of hull material depends on specific requirements, but its versatility allows for the design and production of various vessel types, from high-performance speedboats to large luxury yachts.
Conclusion
Wooden hulls, with their classic form, held sway for generations, while the advent of fiberglass revolutionized yacht construction, introducing a lighter, more durable material that brought about significant advancements in both performance and maintenance.
The subsequent use of aluminum and advanced composites marked another significant shift. Aluminum, prized for its strength-to-weight ratio, and advanced composites, blending materials like carbon fiber, brought increased flexibility in design.
Throughout these transitions, the commitment to enhancing performance has been a driving force, with modern hull designs prioritizing efficiency, speed, and maneuverability, influenced not only by material advancements but also by innovations in hydrodynamics, propulsion systems, and naval architecture.